Views: 182
Vinyl tarpaulin material is a highly durable and versatile material that is widely used in a variety of applications. It is made from polyvinyl chloride (PVC) and is often referred to as PVC tarpaulin. This material is known for its excellent resistance to water, UV rays, and mildew, making it ideal for use in outdoor applications.
Vinyl tarpaulin material is commonly used as a cover for boats, trailers, and trucks. It is also used in the construction industry for scaffolding, as a temporary shelter, and to cover building materials. Additionally, it is used as a tent material for outdoor events and camping trips.
One of the main advantages of vinyl tarpaulin material is its strength and durability. It is resistant to punctures, tears, and abrasions, which makes it ideal for use in harsh environments. Additionally, it is flexible and easy to handle, making it easy to install and transport.
Vinyl tarpaulin material is available in a variety of colors and thicknesses to suit specific needs. It can be made to be opaque, translucent, or transparent, depending on the application. It is also available in flame-retardant varieties, making it ideal for use in applications that require fire resistance.
Another advantage of vinyl tarpaulin material is its affordability. It is a cost-effective alternative to other materials such as canvas, which can be more expensive. Additionally, it requires very little maintenance and can be easily cleaned with soap and water.
However, there are some disadvantages to using vinyl tarpaulin material. One of the main disadvantages is that it is not environmentally friendly. PVC is a plastic material that is not biodegradable and can release harmful chemicals when it is burned. Additionally, it can be difficult to dispose of properly, which can lead to environmental pollution.
In conclusion, vinyl tarpaulin material is a durable and versatile material that is widely used in various applications. It is affordable, easy to handle, and resistant to water, UV rays, and mildew. However, it is not environmentally friendly, and its use should be limited to applications where other materials are not suitable.
Views: 284
Today’s outdoor fabrics are nothing like the outdoor fabrics of old. Outdoor fabrics have come a long way since barkcloth, oilcloth, and vinyl. We now have a multitude of outdoor fabrics made from superior materials, such as 100% solution-dyed acrylic and 100% high UV-resistant polyester. Not only are there better outdoor fabric materials, but there is also a variety of outdoor fabric styles to perfectly coordinate with your décor, including bright colors, stunning patterns, and intricate textures.
Can I Use Indoor Fabric Outdoors?
Sure, but don’t expect your cushions and pillows to last long! Indoor fabric colors bleed when wet and fade easily. Unlike many indoor fabrics, outdoor fabrics are designed with longevity in mind. Outdoor fabrics are made to withstand UV rays, precipitation, pollen, dirt, and mildew. They are easily cleaned by simply brushing off dirt or by using a solution of mild soap and water.
Can I Use Outdoor Fabric Indoors?
Yes! In fact, in many situations, outdoor fabric is probably best. Because it’s stain- and water-repellent as well as easy to clean, outdoor fabric is an excellent option for homes with children, pets, and high-traffic areas. And because outdoor fabric is tough against fading, it is great for furniture situated near windows. If you are thinking that outdoor fabrics are scratchy and stiff, that’s no longer the case. Many of today’s outdoor fabrics feature soft textured weaves and jacquards.
Is There a Difference Between Outdoor Fabric Brands?
Yes. Not all outdoor fabrics are created equally. While the majority of the outdoor fabrics produced today are made of synthetic materials, each brand uses a different manufacturing process or provides a different textile blend. Some of the most popular outdoor fabric types include 100% solution-dyed acrylic and 100% high UV polyester. Because these fabrics are made of synthetic fibers, they are both mildew- and mold-resistant. Each fabric brand carries different warranties on fading. Brands with fabric made from 100% solution-dyed acrylic carry warranties ranging from 5-6 years while brands featuring 100% high UV polyester have a 3-year warranty.
One of the most well-known outdoor fabric brands is Sunbrella, which is made with 100% solution-dyed acrylic yarns. However, other brands, like Outdura, PARA` Tempotest, and Robert Allen Open Air are also made of the same type of material. The manufacturing process of these fabrics is what makes these brands so exceptional. During the solution-dyed acrylic yarn making process, color is added to the acrylic fibers while they are still in a liquid state, giving the fabrics long-lasting color. . Also during production, the fabric is treated with a stain- and water-repellent finish. 303 Fabric Guard replaces this finish if it has been removed after cleaning.
Al Fresco Functional Fabrics are made from 100% high UV-resistant polyester. Unlike many polyester outdoor fabrics, Al Fresco fabrics are not screen printed. Instead, the yarns are woven, creating a lasting design with a higher resistance to fading. Although 100% solution-dyed acrylic fabrics have a better warranty against fading, some Al Fresco fabrics, like the Cabana Stripes and Denims, pass an impressive 117,000 double rubs.
Which Outdoor Fabric Should I Choose?
Choosing the right outdoor fabric depends on how you plan to use it. Solution-dyed acrylic and woven polyester work well for all indoor and outdoor throw pillows and drapes. For cushions, upholstery, or other frequently used items, 100% solution-dyed acrylic and Al Fresco’s fabric that passes 117,000 double rubs are best. Anything that will spend extensive hours in the sun should be made with 100% solution-dyed acrylic because of its high UV rating.
Overall, the best fabric is the one you love most. Now that there is a wealth of options, it is easier to find a favorite fabric that is suitable for outdoors.
Views: 213
Outdoor fabrics differ from indoor fabrics in that they are made to be more durable, and they undergo a chemical treatment process during manufacturing that ensures they will resist stains and mildew. Outdoor fabrics are woven fibers that differ in strength and durability. The primary difference between each type of the most commonly used outdoor fabric lies in the manufacturing process and the fibers that they are made from.
Solution-Dyed Acrylics
Solution-dyed acrylics are fabrics that are dyed before the yarn is created. Most fabrics begin colorless, and then the fibers are woven into yarn, and the yarn is dyed before it is woven into a fabric. With solution-dyed acrylic, a liquid acrylic solution is mixed with the dye, and then it is formed into a fiber so it already has color before it is spun into a yarn. This process makes it color-fast and water-resistant. Solution-dyed acrylics are soft and breathable like canvas and are commonly used in awnings and patio umbrellas, but a softer, more porous version is also used for outdoor pillows and cushions.
Acrylic-Coated Polyesters
Acrylic is used as a base for many outdoor fabrics because of its durability and resistance to wrinkling, fading, and mildew growth. Polyester shares may of these properties, and the use of both fabrics in one material makes a durable outdoor fabric. To make acrylic-coated polyester, the fabric threads are woven first and then the material is dipped into an acrylic coating to color it. This fabric is also available in cotton-polyester blends, which typically have a more appealing appearance. Acrylic-coated polyester and cotton-polyester blends are typically used to make boat and car protectors but may also be used as patio umbrellas and awnings.
Vinyl-Coated Synthetic Fiber Mesh
Vinyl-coated synthetic fiber mesh is also referred to as PVC mesh or slingable fabric. It is often used for sling-type outdoor chairs, whose fabric — not the frame — supports your weight. This fabric is strong and does not stretch. Other fabrics, such as solution-dyed acrylic, printed polyester and printed acrylic outdoor fabrics, are not strong enough to cover these types of chairs. Most PVC mesh fabrics are made of vinyl-coated polyester or acrylic yarns, as well as other synthetics such as olefin and PVC, but the composition of materials varies depending on the manufacturer. They make a durable, easy-to-clean, colorfast and strong outdoor fabric that doesn’t promote mildew growth.
Olefin
Olefin is a manmade fiber that is typically used along with other fibers to create outdoor fabric blends. It is often used in outdoor furniture and for a variety of other applications, including house wrap, marine coverings and clothing. Depending on its chemical structure, olefin may also be referred to as polyethylene or polypropylene. It is manufactured in a similar manner as polyester and nylon. The chemicals used are melted and fed through a shower-head-like device called a spinneret head to form long fibers. Olefin typically has a smooth texture and is usually solution-dyed. It is a durable fabric that dries quickly and resistant to weathering, chemicals, stains and mildew.
Canvas
Canvas is a strong, heavy-duty outdoor fabric used to make sails, tents, backpacks, tarps and even canoes. Modern canvas fabrics may be made from a variety of materials but are usually made using cotton or linen. Canvas is also a generic terms used to describe a variety of outdoor fabrics, including polyester, acrylics and blends of these materials. Mold and mildew are a major drawback of cotton or linen-based canvas fabrics because many true canvas materials are made of natural fibers.
Views: 92
Roller blinds are a popular choice amongst homeowners, favoured for their attractive and fresh design. They are very versatile and can suit and enhance any type of interior décor. Roller blinds are also very functional when it comes to controlling (or blocking out) light, providing privacy and good insulation.
Roller blinds come in many different designs and materials, so there’s plenty of choice when it comes to styling your home!
Some of the most popular styles include:
- Blockout roller blinds
- Light filtering roller blinds
- Sunscreen roller blinds
These designs are all available in different colours and materials. They also have wonderful UV ratings to protect furnishings in your house.
Rooms Where Blockout Roller Blinds Are Most Often Used
Bedrooms
Blockout roller blinds are perfect when installed in bedrooms. Blockout fabrics are very good at offering privacy and blocking out unwanted light during the day or night. When the blinds are rolled down, you can enjoy high levels of privacy in your bedroom.
Kitchens
Blockout and sunscreen fabrics are the two most preferred types for kitchen window blinds. Which of the two you choose comes down to your desired level of privacy. Using water-resistant materials for kitchen windows is also a good idea to prevent damage and unsightly stains.
Living Rooms
Most homeowners use all three types of roller fabrics together in their living areas. In fact, they may use combination brackets and install dual roller blinds to allow the use of any roller at any time. The sunscreen option is usually used during the day when the sun is shining, while the blockout roller option is used at night when darkness sets in.
Offices
Office spaces usually have sunscreen roller blinds installed on their windows. This is because they are effective at reducing sun glare, light and heat during the day. Blockout roller blinds can also be installed in conference rooms where light reduction may be necessary.
Bathrooms
These rooms require a high level of privacy, so blockout materials are the most common choice. When choosing materials for a bathroom, consider choosing a water-resistant material. Light filtering rollers could also be ideal because they offer both light and privacy.
Views: 1694
When you’re looking to purchase a new projector screen, then there are some things that you’ll want to think about first. Getting the right size screen is important, as well as the method it uses to stand up or retract. But, you should also consider what fabric and material the screen is made out of.
If you want a truly good experience with your projector, then using the right screen fabric with it is essential. But what is the best fabric to use for a screen projector? Well, we’re going to look at some of the fabrics that you can use with a projector screen to give the best experience.
Which fabric is best for a projector screen?
If you’re looking for the best fabric for a projector screen, then the right answer is to use a white blackout cloth. You can pick this up for a very reasonable price, and you can can even choose to paint your blackout cloth to create an even better experience.
You can usually pick up this kind of blackout cloth online, or from your local hardware store. Getting the right cloth is important for your picture quality. Plus, if you make it yourself, you’ll need to put in some effort to get the right aspect ratio.
Though I think it’s the best, this isn’t the only material that you can use as a projector screen. So, let’s look at some of the best options out there so you can find the right one to suit you.
Blackout Cloth
If you’ve ever worked the night shift, then you’ll know what material I’m referring to here. It’s the same material used for blackout curtains, and it’s designed to specifically keep out light – it’s made from cotton and polyester. It also works really well as a projector screen, as it’s non reflective and it can be viewed from any angle.
As I also mentioned, you can actually choose to add some paint to your blackout cloth to give it an even better appearance. Whilst you could do this with a roller, it’s probably a better idea to use some spray paint on the cloth. You also might want to use some primer too, which should give you an even better finish.
If you’re looking to make your own projector screen, then this isn the best material to use. However, there are other options out there too that can work as a makeshift fabric for your projector. One good idea is to use roller blinds, which can make for a good projector screen material.
Paint/Wall
Although the majority of the time you’re going to want to use a sort of fabric as your screen, there’s also another alternative which has no fabric at all. I’m talking about using paint as the screen itself, as you can get specially made paint that’s designed specifically for projecting images onto it.
The colour that you use for the paint is going to be important. Most people tend to opt for a white colour as you’d expect. You can also look at going for a black or grey colour too, and it will all depend on the time and ambience of the room when you’re going to use the projector.
You’ll also have to consider the style of the paint you’re using as well. If you use matte paint, then the picture can be a little dark and there will be no vibrancy in the image. On the other hand, if you use glossy paint, then it is going to be too reflective.
From a negative perspective, with a wall you’re not going to have complete control over how smooth the surface is. A screen is very smooth, but your wall may have little bumps and nicks in it that may effect the quality of your viewing.
Other Options
These are the best options for those looking for a DIY solution. But, there are other materials out there you can use, and that are used by larger companies making screens professionally. Here are a few of them.
Conclusion
In conclusion, the best option if you’re looking for a good material to use as a projector screen is a type of blackout cloth. This fabric isn’t particularly expensive, and can easily be used to create a DIY projector screen.
The thing is with DIY screens is that they can take a little while to make, and if you’re not entirely sure on the colour screen you need, this can make it even more difficult.
Of course, you could also avoid creating your own DIY screen and opt to purchase one ready made. Nowadays, screens are more reasonably priced than ever, and you might even be able to get one for not much more than it would cost to do it yourself.
Views: 420
The main difference between laminates and PVC coated material is in how the components are held together. Laminate material is held together by fusing or rolling a top and bottom material around the base cloth, simply fusing the laminate coating layers to each other through the open spaces of the base cloth. PVC coating, however, is bonded to the base fabric by using a special adhesive process.The first step in this process is to spread a high strength adhesive in and around each base cloth thread. Then the PVC coated material, which is in a liquid state, is spread over the glue. Finally they are all fused together using heat and pressure.
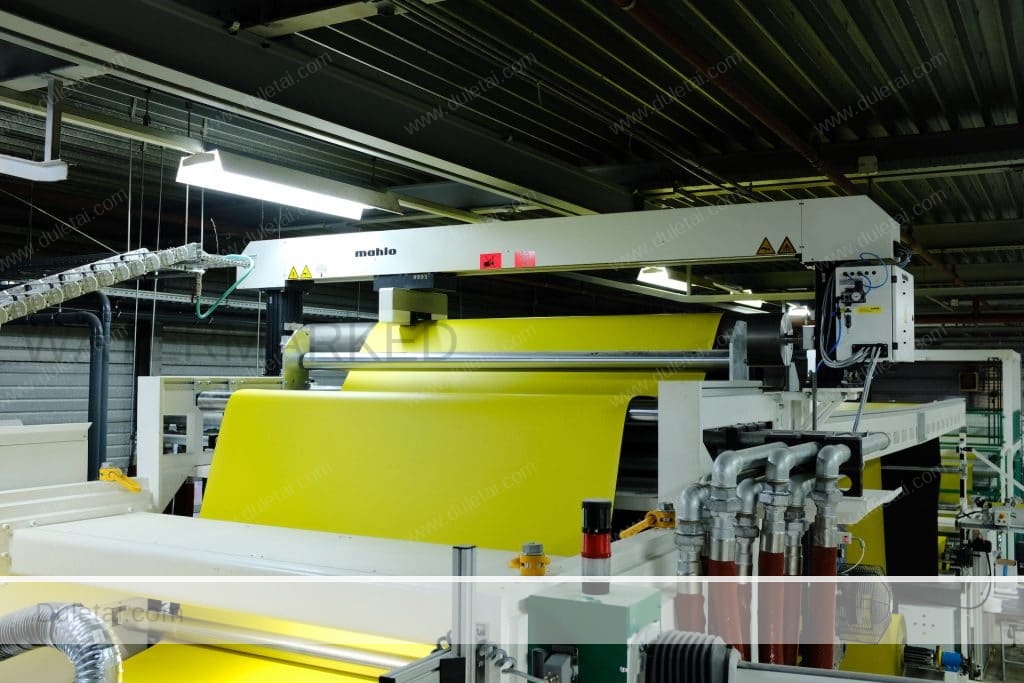
Laminated PVC is composed of a base polyester scrim that is placed between two or more layers of PVC film. These multiple layers of material in huge roll form are fused together in a PVC Laminating machine using extreme pressure and heat to create one solid piece of fabric. Often opaque layers and adhesives are additionally used to attain desired specifications. The formed material is passed over rollers to create the desired finished appearance (i.e. glossy, matte, etc.). The thickness of the raw PVC film on each side of the scrim added to the base fabric (scrim) result in a desired finished weight can add to its performance under Ultraviolet (UV) conditions (on the top side of the laminate) and abrasion resistance (on the bottom side of the laminate).
As a result of the application of a consistent layer/thickness of film on each side of the fabric, the film will fill into the hills and valleys of the base fabric creating a rougher texture (usually on the back side of the fabric). The narrower the openings of the mesh (base fabric) causes a reduction in the depth of the hills and valleys to fill and result a smoother the final appearance of the finished product. Unfortunately, the narrower the openings in the base fabric will in turn decrease the adhesion of the film to itself resulting in “delamination” or poor welding performance. Increasing the thickness of the PVC film will also result in a smoother product but will also add more weight to the finished fabric
Most all vinyl used in the construction of tents is inherently flame retardant, meaning that no additional flame retardant treatment is ever necessary during the lifetime of the fabric. Laminated fabrics are commonly used in the following weights: 12oz/sqyd, 16oz/sqyd, 18oz/sqyd and can be fabricated in any range from 10oz to 28oz.
PVC coated material is composed of a similar base polyester fabric that is passed through molten liquid vinyl and then extruded (or shaved) down to the desired thickness. As with laminated fabrics the coated formed material is passed over rollers to create the desired finished appearance. The resulting fabric is generally smoother on both sides when compared to laminate PVC. The thickness of the raw PVC film on each side of the scrim added to the base fabric (scrim) result in a desired finished weight can add to its performance under Ultraviolet (UW) conditions (on the top side of the laminate) and abrasion resistance (on the bottom side of the fabric).
The result of the extrusion or shaving of the PVC to the base fabric creates a PVC layer that is contoured to the base fabric, filling the valleys with PVC while the exposed surface remains very smooth.
Most all vinyl used in the construction of tents is inherently flame retardant meaning that no additional treatment is ever necessary during the lifetime of the fabric. PVC coated material are commonly used in the following weights: 18oz/sqyd, 20oz/sqyd, 24oz/sqyd and can be fabricated in any range from 16oz/sqyd to 32oz/sqyd.
Benefits & Draw Backs:
Laminated Fabrics:
Benefits
• Lower cost
• Greater availability (Domestic Production)
• Greater color selection
• Less stringent parameters for special order runs (often around 500yd minimums)
• Higher strength to weight ratio-Both tensile and tear strengths
• Most domestic patterning is based on 61” width goods (all manufacturers)
Drawbacks
• Rougher under side of fabric, less easy to clean
• Less resistance to pin holes (as a result of less PVC in the fabric)
• Less pliable with age (as a result of less PVC in the fabric)
Coated Fabrics:
Benefits
• Smoother finish (easier to clean)
• High tensile strength
• Greater durability
• Greater resistance to pinholes
• More pliable in cold weather conditions
Drawbacks:
• Higher cost – (weak Dollar, transportation, lead time, etc.)
• No domestic production
• Stringent parameters for special order runs (often around 5500yd minimums)
• Very few color options
• Fewer weights to choose from
• Weaker tear strength
Views: 44
Antistatic PVC is used for products where surfaces require the reduction or elimination of the build-up of static electricity to avoid damage resultant from the static electrical charges. The role of the anti-static agent is to make the surface of the material itself slightly conductive. Static dissipative PVC is used in varied applications, the most popular being in static electric sensitive areas, electronic manufacturing, industry and mining.
PVC is an ethylene – based polymer, its material is a non – crystalline material. PVC materials are often used with stabilizers, lubricants, auxiliary processing agents, color materials, shock absorbers and other additives. It has non-flammability, high strength, weather resistance and good geometrical stability. PVC has strong resistance to oxidants, reducing agents and strong acids. However, it can be corroded by concentrated oxidizing acids such as concentrated sulfuric acid and concentrated nitric acid and is not suitable for contact with aromatic hydrocarbons and chlorinated hydrocarbons.
Application:
- Equipment cover, dust-free box, test fixture, dust-free room and other places that need antistatic treatment.
- Confined space air changing
- Ventilating tasks & vessels prior to entry
- General ventilation
- Blowing or extracting air
- In combination with Heater to provide warm air
- In combination with Filter Unit to provide clean air
Views: 31
Durability benefits of PTFE coated fiberglass
- Lifespan exceeding 30 years
- Can withstand temperatures of -100 F to +450 F (-73 C to +232 C)
- Tensile strength of 500,000 PSI (more than 10 times the tensile strength of steel)
- Chemically inert
- Weather-resistant
- Resistant to micro-organisms
- Moisture-resistant
- Immune to UV degradation
- Resists the build-up of environmental pollution
- Does not discolor over time
- Does not become brittle over time
Environmental benefits of PTFE coated fiberglass
- Energy Star rated
- Cool Roof Rating Council certified
- PTFE coated fiberglass membranes reflect up to 73% of solar heat and hold only 7% on their exterior surface
- PTFE coated fiberglass provides thermal insulation to a degree similar to conventional glazing
- U value of approximately 4.0-5.0 for a single-layer application
- High shading coefficient, resulting in energy savings over traditional glass glazing
Lighting benefits of PTFE coated fiberglass
- Highly transparent
- It allows natural daylight to reach the people below while also providing shading
- It is translucent, but still screens out ultraviolet rays and excess heat
- Reflects 75% of sunlight
- Absorbs 10% of sunlight
- Transmits 15% of sunlight
Maintenance benefits of PTFE coated fiberglass
- Regularly self-cleaning with rainwater
- A manual clean every 2-5 years is recommended, but because the fabric strength can support human weight, this can be done easily with jet-washers or soft brushes and access to the roof
- No internal cleaning required
- PTFE coated fiberglass installs in a buff color and bleaches to a bright white with sun exposure, so the structure self-maintains a bright white appearance over time
Safety benefits of PTFE coated fiberglass
- US Fire-Rated Noncombustible ASTM E-136, Class A Smoke ASTM E-84, Burning Brand E-108, CSFM Title 19, Pass NFPA 701
- Inherently non-flammable
- Class 1 rating in surface spread of flame testing
- UK Class 0 performance in BS476 pt6 fire propagation tests
Design benefits of PTFE coated fiberglass
- Flexible
- Lightweight (approximately 0.3 pounds per square foot, or 1.5kg per square meter)
- Single panels can be fabricated in almost any size and shape
- Large spans can be reinforced with structural cables
- PTFE coated fiberglass has highly elastic properties (10.5 x 106 PSI modular elasticity)
- It does not significantly expand or shrink under stress
- It provides a significant degree of noise absorption and sound attenuation
- PTFE coated fiberglass can support up to 1,000 pounds per square inch (18 kg per mm)
- It can become a stage for beautiful and dramatic lighting effects
Views: 170
Tarpaulin tearing strength by the trouser tear method
1. Scope
This standard specifies a method of determining the tarpaulin tearing strength under specified conditions. It is applicable to products that, because of their flexibility, do not tear when clamped between the grips of a tensile testing machine. The method makes it possible to compare samples of different products provided their thickness does not differ by more than 10%.
2. Normative references
This standard incorporates, by dated or undated reference, provisions from other publications. These normative references are cited at the appropriate places in the text, and the titles of the publications are listed below. For dated references, subsequent amendments to or revisions of any of these publications apply to this standard only when incorporated in it by amendment or revision. For undated references, the latest edition of the publication referred to applies.
DIN 51220 | General requirements for materials testing machines, including verification and calibra- tion |
DIN 53370
DIN 53515 |
Determining plastic film and sheeting thickness by the stylus method
Determination of tear strength of rubber and plastic film by Graves angle testing with cuts |
DIN EN ISO 291
DIN EN ISO 527-1 |
Plastics – Standard atmospheres for conditioning and testing (ISO 291 : 1997)
Plastics – Determination of tensile properties – Part 1: General principles (ISO 527-1 : 1993 + Corr 1 : 1994) |
DIN EN ISO 7500-1 | Metallic materials – Verification of static uniaxial testing machines – Part 1: Tension/com- pression testing machines – Verification and calibration of the force-measuring system (ISO 7500-1 : 1999) |
3. Concept
Tear resistance
Ratio of the force with which a trapezoidal trouser-shaped specimen as shown in figure 1 resists tear, to the specimen thickness.
Figure 1: Template
Key
- Grip clamping marks
- Incision
4. Specimens
4.1 Sampling and specimen preparation
Specimens as shown in figure 1 shall be cut from the product to be tested. If possible, they shall be taken pap allel and transverse to the manufacturing direction (machine direction) of the film or sheeting so as to permit determination of the tear resistance in both directions as defined by the direction of the incision.
NOTE: If only one piece of the product is available and its manufacturing direction cannot be determined, specimens are to be taken in two directions normal to each other.
The cut directions shall be marked.
The use of a template as shown in figure 2, made of a cut-resistant material, will make it easier to cut out the specimen and make the incision with a knife or razor blade, and to make the grip clamping marks using a pencil, ballpoint pen or grease pencil.
Figure 2: Template
4.2 Number of specimens
A minimum of five specimens shall be tested. If specimens are to tested in both directions, at least five shall be taken for each direction. In arbitration cases, at least ten specimens in each direction are to be tested.
5. Apparatus
5.1 Tensile testing machine
Class 1, as in DIN EN ISO 7500-1, conforming to the requirements of DIN 51220 and fitted with a device for gripping the specimen at the marks (see figure 1).
5.2 Measuring device
For measuring the specimen thickness as in DIN 53370.
6. Procedure
Carry out the tear test in a 23/50 standard atmosphere as in DIN EN ISO 291.
NOTE: In many cases, additional tests performed at lower and higher temperatures are recommended. For this purpose, an environmental test chamber shall be used during testing, capable of maintaining the required temperature to within 0.5 °C
Views: 32
To meet the customers’ over-expected pleasure , now roller blind fabric manufacturers to offer our greatest general service which includes internet marketing, sales, planning, output, quality controlling, packing, warehousing and logistics for Retractable Roller Blind Fabric, Double Roller Blind Zebra Fabric, Black Sunscreen Fabric, Translucent Sunscreen Fabric, We also ensure that your choice is going to be crafted with the highest good quality and dependability. Be sure to feel free of charge to contact us for additional information. We always continually offer you by far the most conscientious customer service, and the widest variety of designs and styles with finest materials. These attempts include the availability of customized designs with speed and dispatch for Retractable Roller Blind Fabric, We strive for excellence, constant improvement and innovation, is committed to make us the “customer trust” and the “first choice of engineering machinery accessories brand” suppliers. Choose us, sharing a win-win situation!
Vinyl roller shades fabric is a four-ply fabric consisting of a piece of polyester scrim laminated between three sheets of polyvinyl film (PVC). Scrim is loosely woven material which made out of polyester. As the material is put through the laminator, it is also embossed. An embossing is the surface texture. Duletai’s most common embossings are matte, taffeta, and polish. Our roller blinds fabrics usually have a matte finish for smoothness. The material is rolled onto a cardboard core. Our standard core size is 3”. The polyvinyl chloride (PVC) films were complemented by polyurethane films and coatings. The width of Vinyl roller shades fabric is from 1.02 m up to 3.20m. Color can be customized according to customers’ requirement. We can produce both hot and cold laminated roller shade fabric, for its good flexibility, excellent tensile strength and tear strength and develop all kinds of durable roller shade fabric for different applications.